
RVS tool qualification for DO-178 B/C and ISO 26262 projects
Simple qualification for critical projects
Our Tool Qualification Kits and Qualified Target Integration Services produce the evidence you need to qualify RVS tools for use in DO-178C or ISO 26262 projects.
We provide expert guidance on how to use the materials we provide to qualify your use of RVS, and clearly identify what you need to do throughout the qualification timeline.
Reduce certification effort
We have qualified the key RVS features that reduce the cost of verifying critical code. Our qualified instrumenters, results data capture, and exports ensure that you don’t need to manually verify any of the results generated by RVS.
Many other features of RVS, including merging coverage data from multiple reports and using justifications to mark your code as covered, are qualified. This lets you streamline your use of RVS and verify your code efficiently in a qualified environment.
Get the best from RVS, qualified
We provide guidance to ensure that you get the best from RVS in a qualified environment, including how to produce evidence that your code meets its timing deadlines, how best to use RVS when your code changes, and how to robustly reuse coverage data across incremental software builds.
We help you keep your project on schedule and avoid lengthy discussions with your certification authority by ensuring that our recommended workflows are aligned with certification guidance.
The Rapita Verification Suite (RVS) has been used in the critical embedded industry for over 15 years and supported a number of avionics projects globally with clients including Airbus, Cobham, Collins, Honeywell and Pilatus. Qualification kits for qualified RVS products have supported more than 20 DO-178B and C certification projects up to and including DAL A.
Ensure that your assurance case remains valid
While we put every effort into ensuring that RVS is as robust as possible, our software may still include bugs. If we identify any issues that may affect your assurance case, for example by producing false positive or negative results or miscalculations in WCET, we notify you about these immediately.
Our Assurance issue notifications include everything you should know about an issue, including a detailed description, fix schedule, and any workarounds, mitigation strategies or fixes we have identified for an issue.
Product features
-
DO-178B/C qualification kit Qualification kits for RVS qualification in DO-178B/C projects.Discover this feature
-
DO-278A qualification kit Qualification kits for RVS qualification in DO-278A projects.Discover this feature
-
ISO 26262 qualification kit Qualification kits for RVS qualification in ISO 26262 projects.Discover this feature
-
Qualified Target Integration Service Additional evidence to qualify the use of RVS in your development environment.Discover this feature
-
Streamlined qualification material Qualification materials are customized to your specific development environment.Discover this feature
-
Template tool user documents Template DO-330 tool user documents to help you write your user documents.Discover this feature
-
Qualified instrumenters Qualified instrumentation that doesn't require manual review.Discover this feature
-
Tool qualification for DO-178 and ISO 26262 Tool qualification support for DO-178B/C and ISO 26262.Discover this feature
-
Clear qualification guidance Understand what you need to do and when to qualify your use of RVS.Discover this feature
-
Compliance checklists Compliance checklists help you identify what you need to do to qualify your use of RVS.Discover this feature
-
Best usage guidance Guidance to get the best from our RVS tools.Discover this feature
-
Assurance issue notification We notify you of issues that may affect the validity of your results as soon as we identify them.Discover this feature
-
Tool qualification licensing Flexible licensing options to best meet your needs.Discover this feature
News & Blog
DO-178B/C tool qualification
If you're using the verification evidence produced by RVS tools to satisfy DO-178B or DO-178C objectives, you'll normally need to show that these tools work correctly within the context of the project's development environment. This is referred to as tool qualification. DO-178B and DO-330 ("Software Tool Considerations", which is referenced from DO-178C) recommend providing the following for tool qualification:
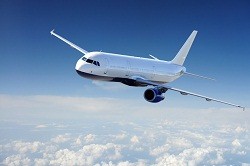
- PSAC (Plan for Software Aspects of Certification). This references the Tool Qualification Plan and the Tool Accomplishment Summary documents. This must be produced by the user of the tool being qualified, per DO-178.
- TOR (Tool Operational Requirements). This describes what the tool does, how it is used and the environment in which it performs.
- TAS (Tool Accomplishment Summary). Shows compliance with the PSAC. Summary of the data showing that all of the requirements in the TOR have been verified. Optional for Tool Qualification Level 5 tools.
- TVR (Tool Verification Results). Test cases, procedures and results demonstrating the TOR is achieved by the tool.
- TQP (Tool Qualification Plan). Describes the process for qualifying the tool, simplifying production of the PSAC. Optional for Tool Qualification Level 5 tools.
Additional documents in Rapita qualification kits
Our qualification kits comply with DO-330 "Software Tool Quality Considerations". To support this, we provide the following additional documents as well as the core DO-178 qualification documents required for tool qualification (less the PSAC), in our qualification kits:
- Tool Qualification Overview – this provides a general overview of how to use the delivered data to comply with DO-330 tool user objectives, per DO-330 table 11-2.
- Tool Qualification Scope – this provides a summary of the tool features that have been verified throughout the qualification process.
- Test Case Design – this provides analysis criteria for the assessment of RVS integrations.
DO-178C objectives addressed by Rapita solutions
Rapita's tools can address many of the DO-178C objectives related to software verification, as shown in Table 1.
ID | Description | Objective | DAL A | DAL B | DAL C | DAL D | Rapita Solution | How? |
---|---|---|---|---|---|---|---|---|
⚫ | ⚪ | ⚪ | ⚪ | ✔ RapiTime* | ||||
⚫ | ⚪ | ⚪ | ✔ RapiTime* | |||||
Executable Object Code complies with high-level requirements | ⚪ | ⚪ | ⚪ | ⚪ | ✔ RapiTest | |||
Executable Object Code is robust with high-level requirements | ⚪ | ⚪ | ⚪ | ⚪ | ✔ RapiTest | |||
⚫ | ⚫ | ⚪ | ✔ RapiTest | |||||
Executable Object Code is robust with low-level requirements | ⚫ | ⚪ | ⚪ | ✔ RapiTest | ||||
⚪ | ⚪ | ⚪ | ⚪ | ✔ RapiTime* | ||||
Test coverage of software structure (modified condition/decision coverage) is achieved | ⚫ | ✔ RapiCover | ||||||
Test coverage of software structure (decision coverage) is achieved | ⚫ | ⚫ | ✔ RapiCover | |||||
Test coverage of software structure (statement coverage) is achieved | ⚫ | ⚫ | ⚪ | ✔ RapiCover | ||||
Test coverage of software structure (data coupling and control coupling) is achieved | ⚫ | ⚫ | ⚪ | ✔ RapiCoupling** | ||||
Verification of additional code, that cannot be traced to Source Code, is achieved | ⚫ | ✔ RapiCoverZero |
⚪ Objective required at DAL
⚫ Objective required with independence at DAL
* - Objective relates to multiple aspects; RapiTime only addresses timing aspects
** - RapiCoupling is currently in development
A(M)C 20-193 objectives addressed by Rapita solutions
The A(M)C 20-193 defines specific objectives to help avionics developers certify systems using multicore processors. These objectives are addressed by the components of Rapita's MACH178, as shown in Table 2.
A(M)C 20-193 objective | Rapita solution |
---|---|
MCP_Planning_1 | MACH178 |
MCP_Planning_2 | |
MCP_Resource_Usage_1 | |
MCP_Resource_Usage_2 | |
MCP_Resource_Usage_3 | |
MCP_Resource_Usage_4 | |
MCP_Software_1 | |
MCP_Software_2 | |
MCP_Error_Handling_1 | |
MCP_Accomplishment_Summary |
Frequently asked questions
-
What if you discover a tool bug after qualification?
We regularly announce tool bugs that could affect existing integrations, when those bugs affect the assurance of the tool output. This includes false positives, missed code constructs (for coverage analysis) and unwanted functional changes to the software under test. We provide advice, workarounds and fix schedules for all assurance issues that we publish this way.
-
What if I discover a tool bug after qualification?
We’ll run the bug through our usual problem reporting, triage and assurance issue analysis processes. If you cannot use a workaround, we can provide add-on fixes or new wavefront versions of the tool that fix your issue, depending on your needs.
-
What is tool qualification and why do I need to do it?
Tool qualification provides evidence that the software you’re using doesn’t introduce or fail to detect errors in your software when it is being used within your project. If you’re working in the context of safety standards such as DO-178 or ISO 26262, you need to provide this evidence if the tool you’re using automates or replaces a manual process and you aren't manually reviewing output from the tool.
-
Which safety standards do you offer qualification support for?
We offer tool qualification support for DO-178B, DO-178C, DO-278A and ISO 26262 safety standards.
-
I’m interested in your full qualification package. Can you describe the process?
We’ve described this in our Tool Qualification Product Briefs.
-
What standards do you use for tool qualification?
We produce our qualification material to support DO-178C, DO-278A and ISO 26262 certification in alignment with guidelines in RTCA’s DO-330: Software Tool Qualification Considerations.
-
Which input languages to the RVS tools can be qualified?
RVS tool qualification covers the use of RVS in projects written in Ada, C and C++, including mixed language projects.
-
Which RVS tools do you provide qualification support for?
The qualification support we already have available is listed on our Resources page. If you need qualification support that isn’t listed, contact us to see how we can help.
-
You don’t offer qualification support for using the RVS tool I’m using in my safety context. What can I do?
If you want qualification support for using an RVS tool in a specific safety context and we don’t already offer qualification support for this combination, we’d be happy to hear from you to discuss extending our support. Contact us for more information.
-
Can you help me provide all of the evidence I need to qualify RVS for use in my project?
We follow the DO-330/ED-215 guidance for qualification of a COTS (commercial off-the-shelf) tool. Per these standards, a tool vendor cannot provide all of the evidence needed for tool qualification – some of it must be provided by the tool user.
Our qualified target integration service includes all of the DO-330 tool developer items, as well as documentation and effort to help you to complete DO-330 tool user items.
This includes generic documents, on-site tests and expected results that help you produce a large proportion of the evidence you need for qualification, including all of the documentation that needs to be provided by the tool vendor (us). In addition to what we provide, you will need to run on-site tests, check results against a list of expected results, and produce some documents, such as the user Tool Operation Requirements, yourself. We provide template tool user documents to help you with this.
See our Tool Qualification Product Briefs for more details.
-
Why is your tool qualification process more complex than that for my other tools?
We use flexible tool components and custom integrations to maximize the efficiency of our tools and their compatibility with a wide range of targets and test environments. The price of this flexibility is additional tool qualification work. We’ve split our qualification support into two parts – one for the flexible tool components and one for the custom integration – and we’ve done everything we can to reduce the effort involved in the custom part.
-
What is the scope of your qualification support?
Licenses for our qualification support are valid for a specific version of the RVS tools you’re using, a specific integration of those tools into your development environment, and a specific customer project.
Please contact us if you need to use our qualification kits in multiple projects, or projects with multiple certifications.
-
What if I make a change to my RVS integration after qualification?
If you make a change to the RVS tool version or integration of RVS into your development environment after we have produced qualification materials, we will need to reproduce those materials, which will incur extra costs.
For more information, see our Tool Qualification Product briefs.
-
What if I discover an error in your qualification support?
If it’s a genuine mistake, we can issue an addendum report or reissue any affected documents, as appropriate. If you need a different scope or level of information, that can be accommodated but requires more effort. For more information, contact us.
-
Do you offer support for projects with a long life cycle?
We offer a frozen version support service for qualified RVS integrations, so you can rest assured that you will have access to the version of RVS you're qualifying even if your project has a very long life cycle.
-
How long does the tool qualification process take?
The length of the tool qualification process varies depending on the complexity of your project and integration.
In general, we can deliver a qualified target integration service in around 6 weeks from the submission of a purchase order, subject to any configuration changes and the availability of Rapita engineers.
We confirm the delivery schedule after we receive your purchase order.
Note that changes to the configuration of your integration during the service delivery process may affect engineering effort, delivery dates and costs.
-
How do RVS qualification kits help reduce review effort?
We customize RVS qualification kits to reflect aspects of your development environment in order to reduce review effort. They include documentation, requirements and test results for the specific RVS tools you are using and the programming languages used in your project.
Qualification kits also include tool user document templates and compliance checklists that help you check your compliance with DO-330 tool user objectives.
-
How do RVS qualification kits help me throughout the qualification process?
RVS qualification kits are designed to make the qualification process easier. Each kit includes a qualification timeline that clearly identifies key stages in the process, and compliance checklists help you check your progress.